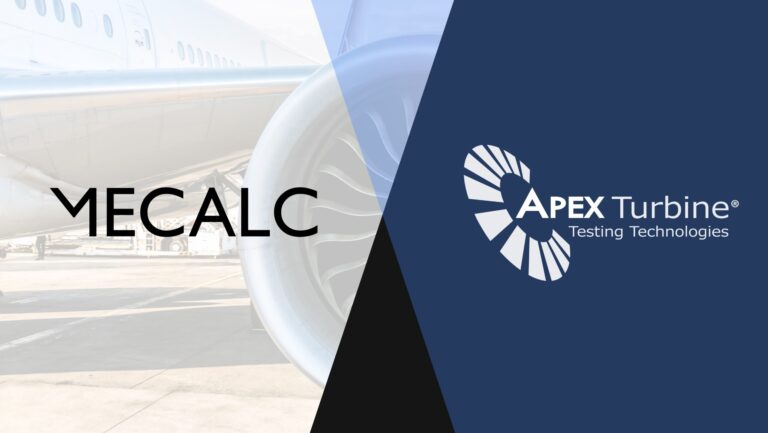
In a significant move to enhance the efficiency and precision of turn-key test and measurement solutions, APEX Turbine Testing Technologies and Mecalc are pleased to announce the extension of their strategic partnership through direct product integration and increased company cooperation. The partnership between APEX and Mecalc brings significant benefits through a direct connect interface between APEX DX+ software and Mecalc hardware, resulting in an improved customer experience and seamless setup of hardware to produce, record, monitor and analyze engineering unit data.
Since 2021, APEX and Mecalc have collaborated to deliver numerous data acquisition channels worldwide, receiving regular positive customer feedback. Last year, APEX utilized a Mecalc QuantusSeries system during on-site test and engineering support for a customer in San Diego. Kurt Nichol, CEO of APEX, praised Mecalc’s system for its advanced performance and impressive form factor. “Our team was able to quickly and easily acquire all the data needed for analysis in just one day. The noise floor was amazingly low, and the system was super reliable. Given consistent positive customer feedback and our own on-site experience, we are excited to announce Mecalc as our preferred hardware partner for data acquisition and control.”
APEX: 25 Years of Integration and Connectivity
APEX provides engineering test software for high-performance data acquisition, analysis, and reporting. Renowned for their aeromechanics test software, APEX is actively expanding into new markets. In 2023, they launched DX+, a versatile software platform for aerospace, propulsion, and power generation testing. DX+ is open and modular, enhancing hardware integration, measurement support, and scalability. It allows for independent component upgrades to meet evolving testing needs. Compatible with other APEX products, DX+ seamlessly integrates with their legacy products: DS, DX, and DR, making it adaptable for various testing environments.
“At APEX, we’ve been developing drivers for 25 years to support a variety of different hardware. With the launch of DX+, we aimed to partner with key suppliers who not only cover the range of measurements our customers need but also provide interfaces that work perfectly with the cutting-edge DX+ architecture,” said Joseph Honea, Director of Software Development and Product Sustainment.
He praised Mecalc’s RESTful interface, emphasizing its “efficient integration capabilities that maximize data output without sacrificing performance. This facilitates seamless data streaming and real-time communication between DX+ and Mecalc hardware, enhancing performance and ensuring reliable data acquisition with a strong emphasis on user experience.”
The DX+ architecture also supports what have become known as “open protocols”, which convert supplier-specific setup information and data streams into a universal format. Although these protocols enable customers to connect to a preferred or custom software application, they can limit performance and reduce data productivity. APEX DX+ architecture uniquely employs advanced data connectivity methods, making it a highly efficient choice for any hardware platform with an open protocol. Its innovative approach ensures superior performance and optimizes data productivity.
Mecalc: Leading Innovators in Data Acquisition Hardware
Mecalc designs, develops, and manufactures advanced data acquisition systems used worldwide for their accuracy and signal conditioning quality. For over 40 years, industries like automotive, aerospace, and defense have relied on Mecalc for key project development and quality control.
Johannes Geyser, Managing Director of Mecalc, shared his enthusiasm for extending the partnership with APEX: “We are excited to continue as one of APEX’s preferred hardware partners. Our hardware combined with their software significantly enhances testing accuracy and efficiency. This partnership reflects our dedication to delivering top solutions to our clients.”
Mecalc’s QuantusSeries products provide data acquisition systems designed to improve phase accuracy, bandwidth, and scalability. These systems measure parameters including sound, vibration, and temperature, and are recognized for their durability and quality. QuantusSeries architecture enables modular upgrades and accessible data, making it adaptable to user needs.
Advancing Hypersonic Testing Together
In July of this year, APEX will install the first fully integrated DX+ and Mecalc QuantusSeries system at the University of Notre Dame’s Turbomachinery Laboratory in preparation for a hypersonic field test at the facility. This is the first of two tests scheduled under an AFWERX Phase 2 STTR program, involving collaboration from APEX, AFRL, AEDC, and the University of Notre Dame’s Turbomachinery Laboratory to advance hypersonics testing.
APEX is enhancing the functionality of DX+ to support comprehensive hypersonic testing. DX+ will be the first APEX product to include high speed video integration, which will improve data analysis by enabling real-time monitoring and post-test synchronization of video with other data. Additionally, APEX will demonstrate advanced modeling and simulation integration capabilities with video streams. This includes opening and displaying model files, rendering contours, mapping sensors, and interpolating sensor data. This modeling and simulation effort aligns with the industry’s move toward a comprehensive digital engineering test solution. Using measurements from Mecalc’s state-of-the-art hardware to drive these real-time models and simulations will seamlessly tie together high-quality traditional measurements with cutting-edge predictive and visualization technology.
Follow us on LinkedIn for updates on our STTR program.
For more information on APEX Turbine Testing Technologies and their software solutions, visit our website.
To learn more about Mecalc and their data acquisition hardware, visit Mecalc’s Website.